Unlimited computing capacity in the cloud and real-time analytics capabilities now enables manufacturers to access new insights and build systems of intelligence. By gathering data from connected devices, and transforming that data into valuable business intelligence, manufacturers can greatly improve operations by implementing a predictive maintenance strategy.
Connecting these intelligent systems with Dynamics 365 for Field Service allows businesses to move from a reactive to proactive model of maintenance.
There are three basic strategies of equipment maintenance: reactive, preventative and predictive maintenance.
1. Reactive Maintenance
The reactive maintenance strategy sees equipment or parts replaced only after they have failed. With this strategy, equipment or parts will have the maximum possible service life. However, waiting for the failure to occur within an approximate timeframe often leads to unplanned down time. Reactive maintenance is not acceptable in scenarios where sudden failure poses a safety risk or could cause damage to related parts or equipment.
The figure below shows the service life in months of 50 devices. The failure of each device is marked by an ‘x’. In this example the service life of devices varies significantly.
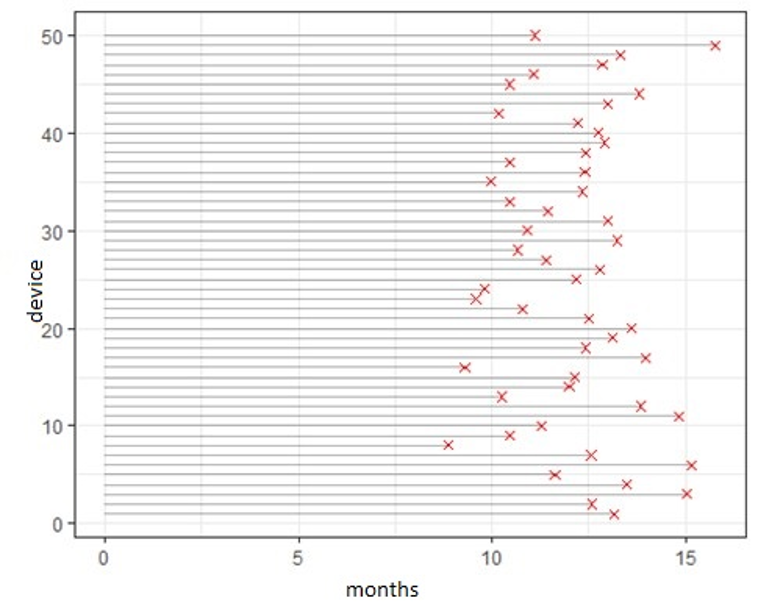
2. Preventative Maintenance
The preventative maintenance strategy sees equipment or parts replaced according to a specific schedule. By scheduling replacement to minimise component failures this scenario reduces safety risks and downtime, yet inevitably wastes valuable service life.
The figure below shows a preventative maintenance schedule applied to the previous example, with device replacement set at a service life of 10 months. A small number of sudden failures still occur, yet most of the devices could have remained in service much longer.
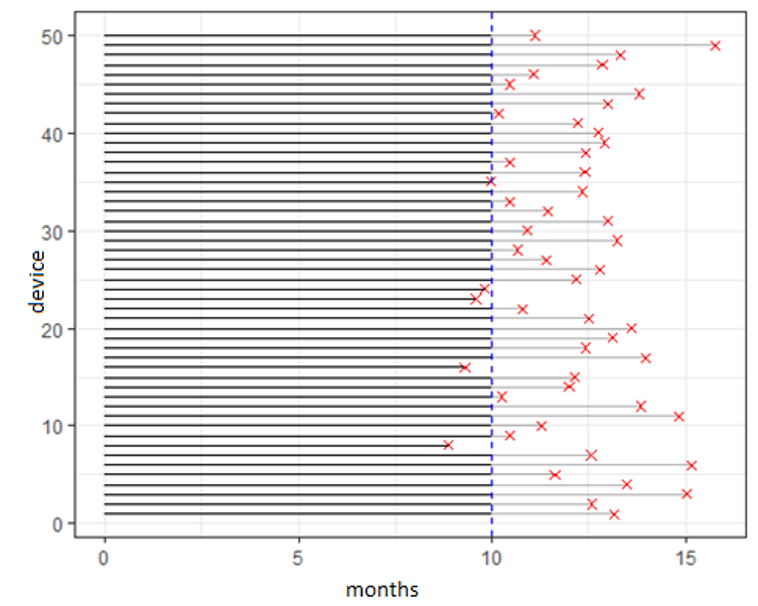
To ensure no failures, the replacement schedule could be shortened. The business will determine what level of device failure is acceptable based on a combination of factors including cost and safety.
3. Predictive Maintenance
The predictive maintenance strategy aims to replace equipment and parts on a just-in-time basis, avoiding unplanned failures and maximising service life. The figure below shows our example where a perfect preventative maintenance schedule has been implemented.
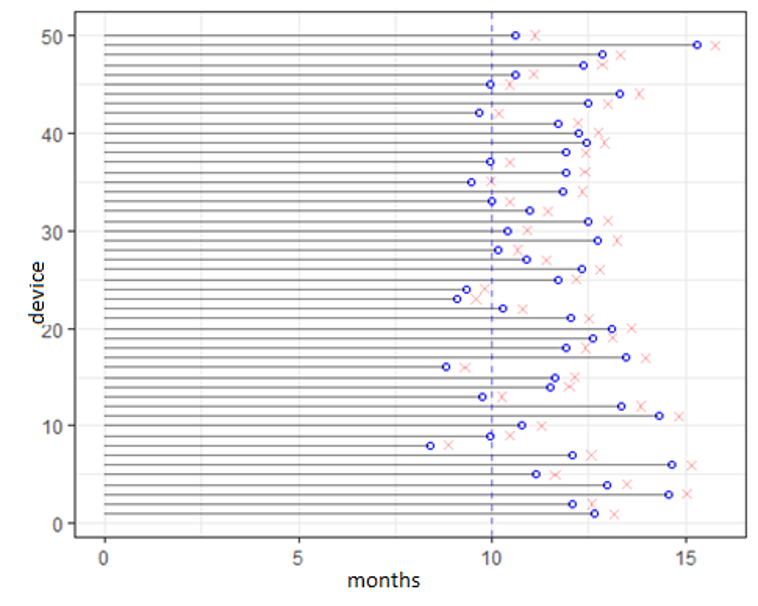
The predictive strategy uses machine learning in a supervised learning process. This learning process requires data – the full life history of a series of devices – to train an AI model. The more complete the service life data, the more accurate the model. To learn to predict failures, the data must contain instances of those failures.
The recently launched Microsoft Azure Machine Learning services (AML) include a Workbench application as well as command-line tools to help develop and manage machine learning solutions through the entire data science life cycle. The Model Management Service allows the deployment of predictive models into a wide variety of environments.
Once a sufficient predictive model has been built and deployed, an Azure IoT Hub is set up to collect data from device sensors, detect anomalies and send alerts to Dynamics 365 for Field Service which triggers a configurable workflow process, for example, to automatically dispatch a field technician.
In our example, a problem arises because a perfect predictive strategy, by definition, removes all failure events from the service data; thus, retraining the AI model with current data is not possible. However, in the real world we can assume that we will be able to add additional models based on data from residual failure events. Also, it may be possible to continue to collect data from a population of devices that remain on a reactive maintenance schedule (for example, customers with different maintenance contracts).
Which strategy is best?
Where reactive and preventative maintenance strategies require some initial analysis, once the strategy is in place, minimal effort is required to maintain the strategy. On the other hand, predictive maintenance strategies require greater on-going input, but enable businesses to repair, clean, or replace parts only when needed. By moving to a predictive maintenance strategy, manufacturers can:
- avoid costly equipment failures
- maximise uptime with better maintenance scheduling
- learn from data to fine-tune processes
- offer customers new proactive maintenance services